來自奧馬哈內布拉斯加大學的研究人員Keaton Young,James E. Pierce和James M. Zuniga在“身體動力,3D打印部分手指假肢的評估:案例研究”中探索通過3D打印製作假肢。在這裡,他們了解更多關於手部假肢如何能夠改變一名72歲男性的部分手指截肢的生活質量。手部的部分損失(例如手指的部分損失)被認為是“輕微的截肢”,到2050年,預計將有近360萬截肢影響個人生活質量。許多假肢能夠極大地幫助改善日常生活,同時改善:
1、心理社會自尊
2、身體形象
3、肢體協調
4、身體勻稱
由於設計較差導致以及截肢者對美學不滿意的自我意識。高達70%的假肢患者報告對他們不滿意。在本研究中檢查的案例研究中,一人右手丟失了部分食指。他以前一直在使用鈦MCP-Driver™手指假肢也取得了一些成功,但這些成本高達9,000美元至19,000美元。鈦裝置將用作本研究中創建的鈦裝置的比較。
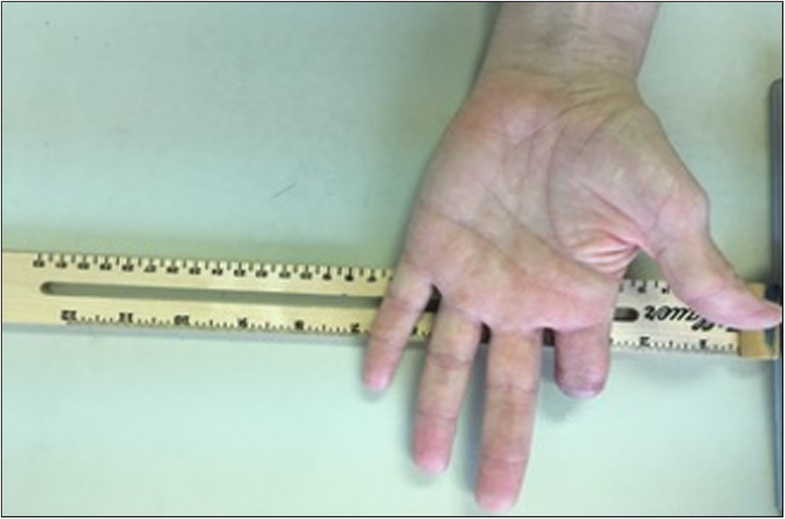
研究對像在左手近端指間關節截肢
隨著病例研究患者手部的虛弱區域以及其他未受影響的手(其作為假體模型)被掃描,配件開始遠程製作。3D打印部件允許通過三個分段部分進行夾緊抓握,其中每個部分之間具有簡單的樞轉接頭。“該設備使用定制的軟氯丁橡膠鑄件固定在手掌上,用於創建一個錨定點,用於驅動設備發生並減少用戶可能從尼龍繩中受到的摩擦力用於在LFP的指間關節周圍產生旋轉力,在指尖上添加一個矽膠手柄,以增加抓握順從性,並防止抓握物體的滑動。假體的初始尺寸是遠程進行的,並開始指導患者拍攝受影響和未受影響的肢體,包括已知的可測量尺度,例如公製網格紙。
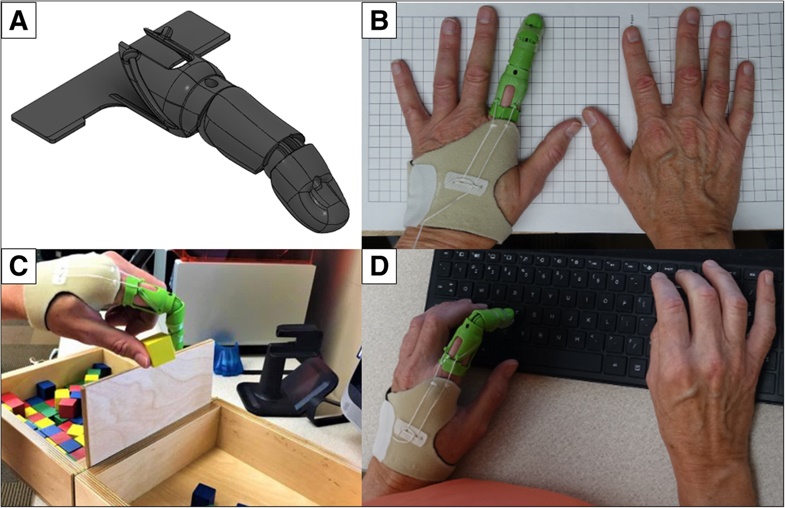
A: 一個渲染的LFP CAD模型。B:使用3D打印的手指假肢在未受影響的手和受影響的手之間手對稱。C:參與者打開箱子測試。D:參與者在電子鍵盤上打字
零件使用Ultimaker 2 3D打印機採用 PLA材料打印,包括其他組件,如尼龍繩和彈性繩,用於彎曲和伸展,以及用於“軟插座”的襯墊形式和用於減少摩擦的保護性覆蓋物。結果令人印象深刻,因為患者的手指能夠在沒有任何假體附著的情況下靈活完成任務。通過對比,使用假肢,他可以移動22 BPM,而未受影響的肢體移動30 BPM。本地3D打印手指假肢(LPF)提供與MFP設備類似的結果,特定於任務的效率提高到73%。研究人員表示,這證明LFP或MFP可以提高用戶的靈活性。
“隨著3D打印的可訪問性不斷擴大,3D打印有很大的潛力為多種新的醫療應用和設備鋪平道路,這可能會改變未來醫療設備的製造過程。”研究人員總結道。
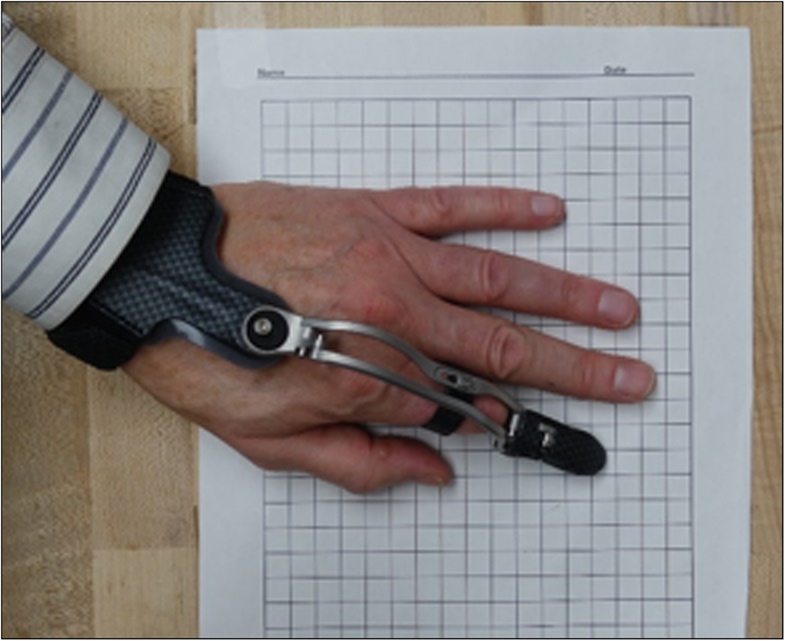
NAKED Prosthetics Inc. MCP驅動器手指假肢 , 失去肢體功能,截肢或處理先天性缺陷意味著他們必須比正常人更努力地做他們認為理所當然的事情,比如走路,跑步,抓物品,吃飯,彈奏樂器。世界各地的設計師利用3D打印的優勢改變了許多人的生活,從假肢到拐杖,輔助戶外活動的設備等,在未來,3D打印必將更好的服務於人們。
(編譯自3Deasy-pitnt.com)如有轉載請列明